The Art and Science of Injection Mold Plastic: Revolutionizing Manufacturing
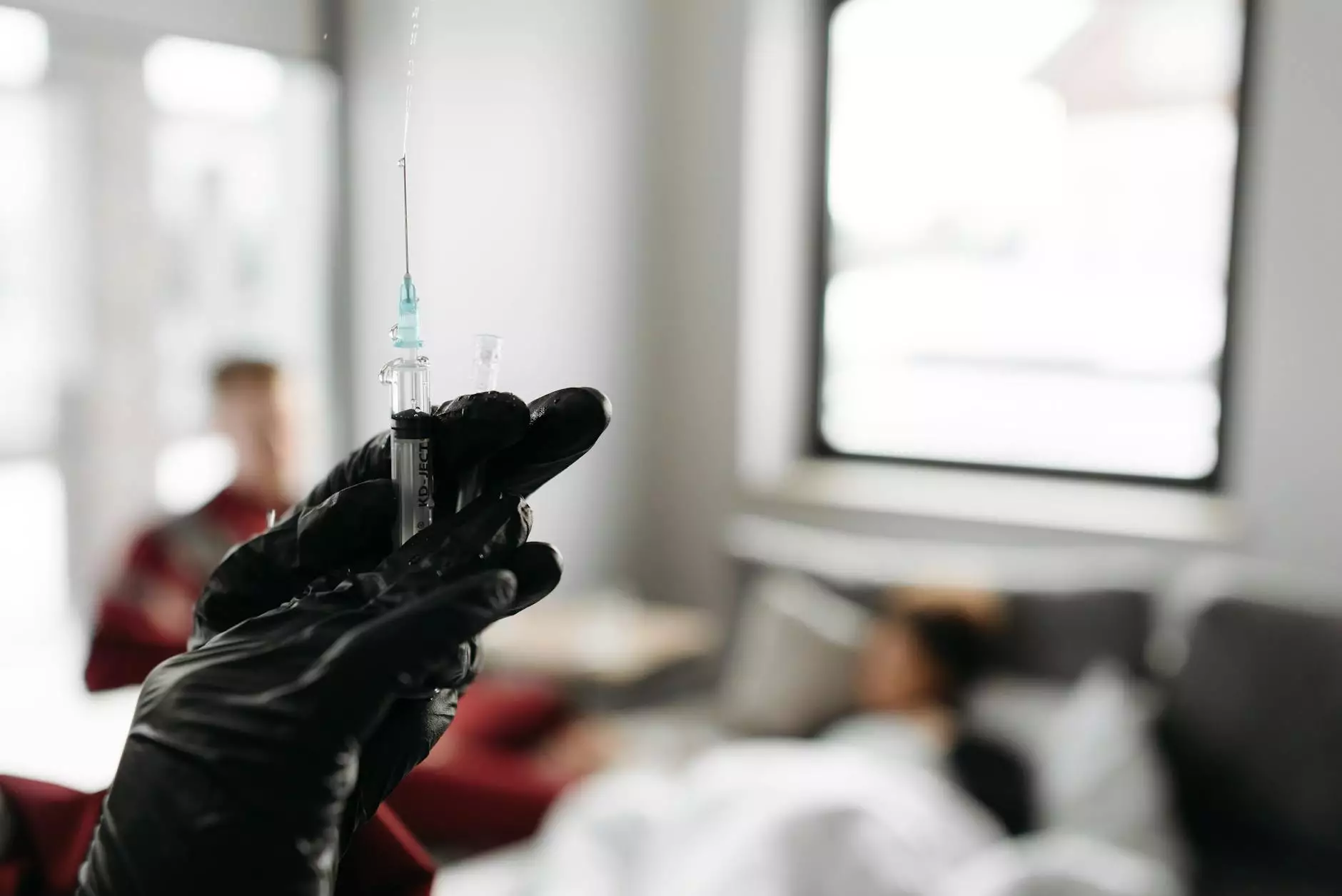
In the dynamic world of manufacturing, the use of injection mold plastic has emerged as a transformative technology that has streamlined production processes and delivered unparalleled precision in product design. This article delves deep into the nuances of injection molding, examining its benefits, applications, and the factors that make it an indispensable part of modern industry.
What is Injection Molding?
Injection molding is a manufacturing process for producing parts by injecting molten material into a mold. The material used can vary widely, but typically, it consists of plastic, which is used extensively in various applications due to its versatility and durability. The core principle of this process involves the following steps:
- Melting: The raw plastic pellets are heated until they reach a molten state.
- Injection: The molten plastic is injected into a mold under high pressure.
- Cooling: Once the mold is filled, the plastic cools down and solidifies.
- Ejection: The cooled, solidified part is ejected from the mold.
Benefits of Injection Mold Plastic
The adoption of injection mold plastic in manufacturing yields a plethora of benefits, making it a preferred choice for many industries. Here are some of the key advantages:
- High Precision: One of the standout features of injection molding is the high level of precision it offers, ensuring that each part is manufactured to accurate specifications, minimizing material waste.
- Speed of Production: Injection molding allows for high-volume production, significantly reducing lead times and getting products to market faster.
- Versatility: With a wide selection of plastic materials and colors available, manufacturers can create a diverse range of products, from intricate designs to simple components.
- Cost-Effectiveness: While the initial setup costs can be high, the long-term savings associated with mass production and efficiency make injection molding a cost-effective solution.
- Scalability: The process is easily scalable, accommodating a small batch of prototypes or large production runs with equal efficiency.
Applications of Injection Mold Plastic
The applications of injection mold plastic are extensive and varied. Here are some prominent industries benefiting from this technology:
1. Automotive Industry
In the automotive sector, manufacturers rely on injection molding for components like dashboards, door panels, and various engine parts, which require both strength and aesthetics.
2. Consumer Products
From toys to home appliances, injection molding allows for the production of durable and colorful consumer goods, providing companies the flexibility to innovate continually.
3. Medical Devices
The medical industry employs injection molded plastics for devices and equipment that must adhere to strict safety and durability standards, such as syringes and surgical tools.
4. Packaging
Injection molding is extensively used in producing packaging solutions, including containers and lids that need precision and durability to protect their contents.
The Role of Metal Fabricators in Injection Molding
As a vital part of the manufacturing ecosystem, metal fabricators play an essential role in injection molding. They are responsible for creating the molds used in the injection molding process. Here are some key points highlighting their contributions:
- Custom Designs: Metal fabricators can create custom molds tailored to specific requirements, ensuring better product fit and functionality.
- Material Selection: The choice of metal used in mold construction is critical, as it affects both the mold's durability and the quality of the molded part.
- Precision Engineering: Fabricators employ advanced machining techniques to produce molds that achieve the required tolerances for high-quality parts.
Challenges in Injection Mold Plastic Manufacturing
Despite its many advantages, the injection mold plastic process is not without challenges. Companies like DeepMould continually seek innovative solutions to address the following industry hurdles:
- Initial Costs: The upfront costs associated with mold design and production can be significant, which may be a barrier for some businesses.
- Material Limitations: While there is a wide range of materials available, the specific properties of each material can limit their applications.
- Design Constraints: Certain design features may be difficult to achieve with injection molding, necessitating careful planning and optimization.
- Cooling Issues: Uneven cooling may lead to warping or structural inconsistencies in the final product, demanding precise control of the molding process.
Future Trends in Injection Molding
The future of injection mold plastic appears promising, with ongoing advancements paving the way for greater efficiency and innovation. Some predicted trends include:
1. Sustainable Practices
As the world increasingly focuses on sustainability, manufacturers are exploring eco-friendly materials and processes that reduce waste and energy consumption.
2. Advanced Materials
Innovations in material science are leading to the development of new plastic compounds that offer improved strength and reduced weight.
3. Automation and Industry 4.0
Integrating automation and smart technologies into injection molding processes enhances efficiency, consistency, and production speed.
Conclusion
In conclusion, the significance of injection mold plastic in manufacturing cannot be overstated. With its unmatched precision, efficiency, and versatility, it stands as a cornerstone of modern production methods. Companies like DeepMould exemplify excellence in the industry by continually pushing the boundaries of what can be achieved with injection molding. As technology evolves, so too will the capabilities of this remarkable process, driving innovation and efficiency across multiple sectors.
To stay ahead in this competitive landscape, it is imperative for businesses to understand the intricacies of injection molding and leverage its benefits to enhance their product offerings. By embracing the future of manufacturing with cutting-edge solutions, companies can not only meet but exceed the expectations of their customers.