Understanding Asphalt Plants: A Comprehensive Overview
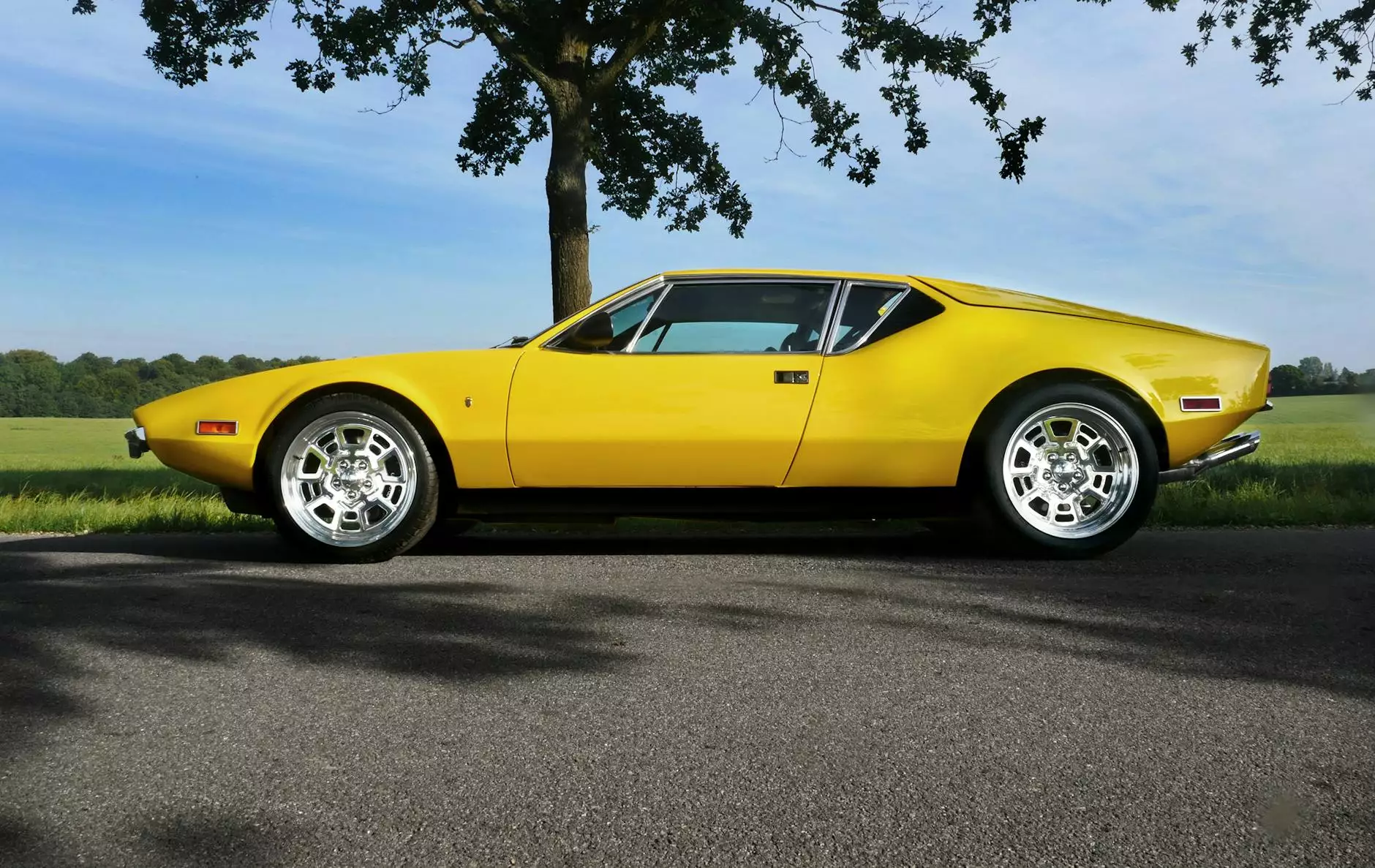
In the realm of construction, infrastructure development, and road-building, the significance of an asphalt plant cannot be overstated. These remarkable facilities play a pivotal role in producing high-quality asphalt mixtures that are essential for various construction projects. This article aims to delve into the fundamental aspects of asphalt plants, highlight their types, components, operational processes, and the myriad of benefits they bring to construction projects.
The Importance of Asphalt Plants in Modern Construction
Asphalt plants serve as the backbone of paving operations and road maintenance. They are the sites where raw materials are transformed into durable asphalt that can withstand vehicular traffic, weather conditions, and time. The following points elucidate the importance of asphalt plants:
- Quality Control: Asphalt plants allow for precise control over the mix design, ensuring that the final product meets specified standards.
- Efficiency: They facilitate the rapid production of asphalt, catering to the high demands of large construction projects.
- Sustainability: Modern asphalt plants often incorporate recycling processes to utilize reclaimed asphalt pavement (RAP), minimizing waste.
- Economic Impact: By producing asphalt locally, these plants reduce transportation costs and contribute to the local economy.
Key Components of an Asphalt Plant
Understanding the key components of an asphalt plant is crucial for comprehending how these facilities operate. Asphalt plants generally consist of several core components:
- Cold Feed Bins: These bins store unprocessed aggregates, ensuring that the right quantities of materials are available for mixing.
- Drying Drum: The drying drum is essential for removing moisture from the aggregates, ensuring that the asphalt binder adheres properly.
- Hot Mix Asphalt Batcher: This component measures and combines the dried aggregates with asphalt binder in precise amounts to produce the desired mix.
- Mixing Unit: The mixing unit blends the aggregates and binder thoroughly, producing a uniform asphalt mixture.
- Storage Silos: After mixing, the asphalt is stored in silos, where it can be kept at optimal temperatures before being transported to the job site.
- Control System: Modern asphalt plants are equipped with sophisticated control systems that monitor and adjust various parameters to optimize production.
Types of Asphalt Plants
Asphalt plants are typically categorized into two main types, each designed to meet specific operational needs and project requirements:
1. Batch Asphalt Plants
Batch asphalt plants produce asphalt in batches, allowing for high flexibility in mix designs. These plants operate on a sequential process, where each batch is produced independently. The benefits of batch plants include:
- Custom Mixes: They can produce varying asphalt mixtures, making them ideal for projects requiring multiple mix types.
- Quality Control: Since each batch is produced separately, it’s easier to control quality and consistency.
2. Continuous Asphalt Plants
Continuous asphalt plants operate in a non-stop mode, providing a constant output of asphalt. These plants are suitable for large-scale operations where efficiency is critical. Some advantages of continuous plants include:
- Higher Output: Continuous plants can produce large quantities of asphalt quickly.
- Lower Operating Costs: They generally require less labor and have lower energy consumption per ton of asphalt produced.
Operational Processes in Asphalt Plants
The operation of an asphalt plant involves several systematic processes, all aimed at ensuring the production of high-quality asphalt. The key stages include:
1. Material Preparation
In this initial stage, the aggregates are fed into the cold feed bins. The materials are carefully selected based on the project specifications, which may include different sizes and types of aggregates.
2. Heating and Drying
The aggregates are then moved to the drying drum, where they are heated. This stage is vital to eliminate any moisture content, which can negatively affect the bonding of the asphalt.
3. Mixing
Once the aggregates are dry, they are mixed with heated asphalt binder in the mixing unit. This blending process ensures that the aggregates are fully coated with the binder, resulting in a homogeneous mixture.
4. Storage and Transport
After mixing, the asphalt is transferred to storage silos where it is kept warm until it is needed. The final step involves transporting the asphalt to the construction site, often through specialized trucks designed to keep the material hot and workable.
Benefits of Using Asphalt from Asphalt Plants
The advantages of using asphalt produced from an asphalt plant are manifold. Some of the key benefits include:
- Durability: Asphalt is known for its robustness and ability to endure heavy traffic and adverse weather conditions.
- Cost-Effectiveness: The long lifespan and low maintenance requirements of asphalt lead to lower overall project costs.
- Quick Installation: Asphalt can be laid and rolled out quickly, enabling faster project completion.
- Environmentally Friendly: Innovations in asphalt production, such as using recycled materials, make it a sustainable choice for paving.
Conclusion: The Future of Asphalt Plants
As we move forward into an era where construction is increasingly focused on sustainability and efficiency, the role of asphalt plants will continue to evolve. Innovations in technology are paving the way for smarter and more efficient plants that prioritize quality and environmental responsibility.
In summary, understanding the functional dynamics and advantages of asphalt plants is crucial for anyone involved in the construction and infrastructure industry. By leveraging the benefits and capabilities of these facilities, businesses can ensure they deliver durable, efficient, and economically viable asphalt solutions for their projects.
References
For more in-depth knowledge about asphalt plants and their operations, check out resources from Polygon Machinery.